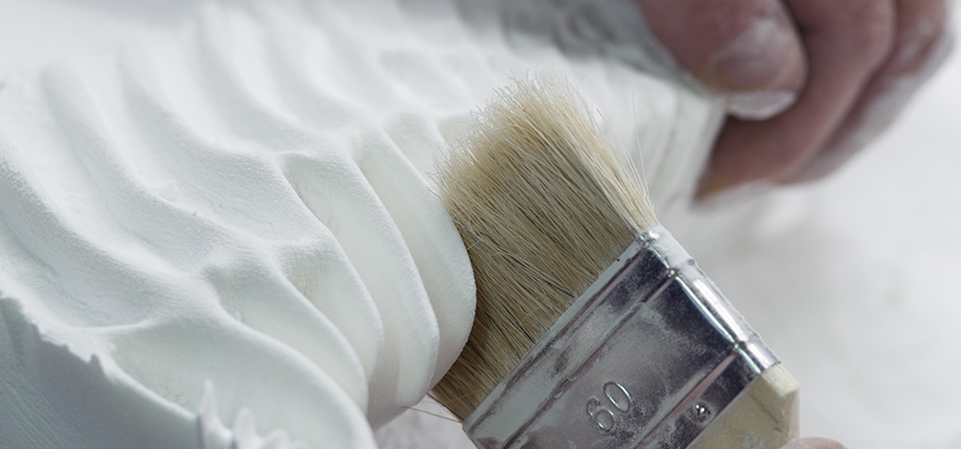
Powder Bed Fusion (Selective Laser Sintering – SLS)
High-Performance Plastic Additive Manufacturing Technology
Selective Laser Sintering (SLS) is a plastic additive manufacturing (AM) process that produces parts from digital files by sintering thermoplastic powders—typically polymers such as polyamide or polystyrene—layer by layer within a preheated build chamber.
Compared to other AM processes, SLS is generally more cost-effective, faster (thanks in part to the absence of support structures), and capable of producing strong, durable mechanical parts. However, SLS parts often have a rough surface texture and may be prone to warping.
SLS is particularly well-suited for rapid prototyping, as well as direct manufacturing of small to medium production runs of complex parts that require high mechanical or thermal resistance. It is also an excellent method for producing patterns used in investment casting (lost wax process).
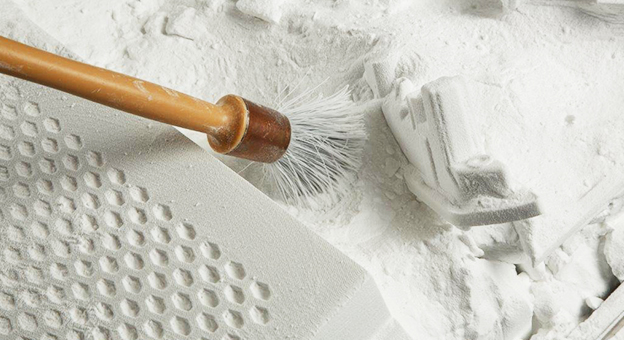
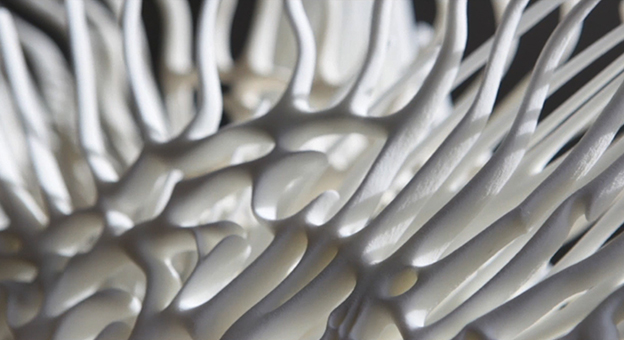
SLS Equipment at MMB VOLUM-e:
- 1x 3D Systems Sinter Pro – Max build size: 505 × 505 × 400 mm
Powder Sintering Materials Library:
Easy to process, compatible with all finishing types.
Heat resistance: 180 °C (95 °C under load)
High stiffness and dimensional stability, good surface quality, suitable for all finishes.
Heat resistance: 179 °C (134 °C under load)
PA haute température (DuraForme HST)
High thermal resistance: 184 °C, 179 °C under load at 182 MPa. Ideal for demanding applications.
TPU
Flexible and durable material for soft-touch or functional parts.
Max dimensions: 505 × 505 × 440 mm
PA souple DuraForm
Rubber-like properties (59 Shore A), limited finishing options.
PA chargé aluminium
Enhanced stiffness and thermal conductivity.
Max dimensions: 505 × 505 × 440 mm
PA ignifugé (PA2241FR EOS) FAR25
Low flammability, compliant with FAR 25 standards. Ideal for safety-critical components.
PA Primecast (EOS)
Burn-out material with excellent surface finish. Perfect for investment casting patterns.